日本自动化科技前沿:将人工智能融合到自动驾驶、半导体产业
【第一对焦:日本】丰田汽车董事长丰田章男宣布:“在硬件领域取得成功的丰田,将变身为融合(AI等)软件技术的新企业。”以AI”明星军团”为后盾,丰田汽车意在掀起汽车,乃至整个移动世界的变革!富士通综合产品战略本部、AI应用咨询部部长山影让表示:“我们想把AI的创新成果立即传递给客户。”瑞萨电子第二解决方案事业本部产业第一事业部、网络解决方案部专家高仓敏说:“AI的优点,是能和人一样,学习波形并判定优劣。”以往,对良品和不良品的判断,是交由熟练技工来完成的。但是,技术人员能够观察到的数据量有限。而且,由于发光强度的波形非常复杂,所以不适合根据阈值进行管理,且难以实现自动化操作。在这一点上,AI可以像技术人员一样从综合角度判断优劣。实际上,通过运用AI技术,不良品的检出率提高了6倍。瑞萨半导体制造技术统括部、流程加工技术部部长秋元健司表示:“如果能在工序内检测出不良品,将有效避免后工序中无意义的加工,从而大幅降低企业成本。”
科技生产与生活:日本科技企业是如何将AI融合到各个领域中的?
科技生产与生活:日本科技企业是如何将AI融合到各个领域中的?下面我们就来仔细聊聊这个话题。
丰田汽车瞄准的,可不仅仅是自动驾驶,而是将AI应用于更广泛的领域。例如,协助视力和判断力下降的老年人驾驶,提升护理用室内机器人、汽车的强度,提高燃料电池的效率,降低材料的开发成本等。在CES现场,丰田汽车甚至还与Preferred Networks等AI研究公司共同展示了具备深度学习、自动驾驶能力的汽车演示——8台自动驾驶车模型互相碰撞后,自动学习如何在行驶时避免碰撞。
每辆车上,都载有检测周围环境的传感器,并以取得的信息为基础,控制油门、刹车、方向盘等。学习机制,是在遇到冲撞时给予处罚,进行强化学习。学习4小时后,汽车就能避免所有碰撞,顺利行驶。该系统的目标,是让自动驾驶汽车能够精准识别其他驾驶汽车(包括人工驾驶汽车)可能发生的冲撞危险,并瞬间避让。
和视野只关注前方的人不同,自动驾驶汽车的后方也装有传感器,当监测到后方有危险时,自动驾驶汽车会毫不犹豫地后退,躲开。丰田汽车董事长丰田章男宣布:“在硬件领域取得成功的丰田,将变身为融合(AI等)软件技术的新企业。”以AI”明星军团”为后盾,丰田汽车意在掀起汽车,乃至整个移动世界的变革!
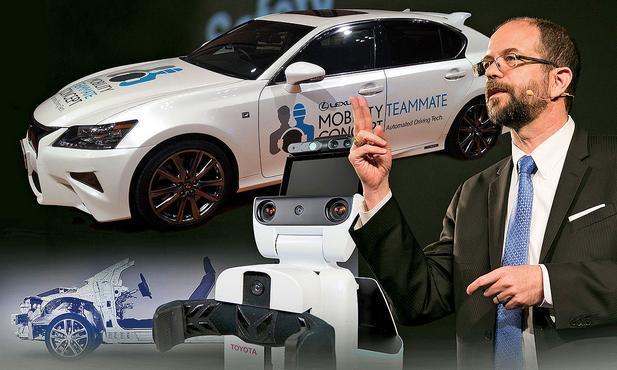
富士通:让新人,也能做专业水平的设计
2015年11月,富士通宣布将本公司的人工智能(AI)技术系统化,并将其命名为“Zinrai”。名字取自成语“疾风迅雷”的日文发音,意思是麻利、雷厉风行。富士通综合产品战略本部、AI应用咨询部部长山影让表示:“我们想把AI的创新成果立即传递给客户。”
通过学习以往积攒的设计数据,AI能够精准识别多层基板的层数。富士通表示,精准估计多层基板的合适层数很难。因为多层基板很难改变中途的结构设计——低估层数,可能导致设计失败;高估层数,可能导致成本上升。也就是说,要在开始详细设计之前,就确定好适当的层数。过去,能做到准确估算合适层数的,只有熟练技工。富士通据此彻查了整个思考过程:面对庞大的设计参数,熟练技工的着眼点是什么?调查结果显示,“零件件数”“引线数”“网络(接线信息)”“基板形状”等参数在层数估算中起了很大作用。
接下来,富士通将这些参数作为特征量,让AI学习以往的设计数据。通过投入AI应用,进入公司第一年的新技工也能达到与熟练技工相同的精准度,估算多层基片的层数。在运用AI之前,富士通曾经研发过一种算法,只要输入设计参数就能输出适当的层数。但是,由于设计参数的组合过于庞大,在人工开发问题上存在一定的局限性。富士通研究所制造技术研究所代理所长涩谷利行表示:“过去,无论怎样改进算法,机器估算的层数结果都无法与人工估算相媲美。但利用AI和大数据后,熟练技工感受到了前所未有的压力。”
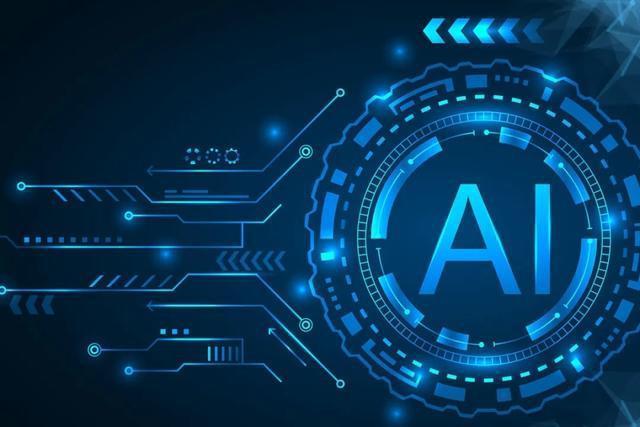
自动编写和修改程序AI在生产领域的应用案例也很多。最常见的,当属生产线检查工序等使用的图像识别程序的制作。例如,在印刷布线基板上安装零件的线路中,拍摄检查工序的基板图像,通过图像识别程序确认特定的零件是否已被正确安装。迄今为止,此程序一般是由技术人员根据图像状态(亮度、对比度等)和基板设计制作而成的。但是,一旦图像状态和基板设计改变,就必须修改程序。这样一来,如果今后继续进行多品种少量生产,势必会出现技术人员紧缺的情况。因此,现场提出了希望能自动制作和修改程序的要求。
富士通利用通过“遗传算法”进行学习的AI,制作并修改程序。起初,AI的实力只能识别、检查零件的基本形状。但现在,AI可以判断实际安装的质量是否合格。主导此次研究的富士通研究所制造业技术研究所特任研究员肥冢哲男表示,AI提取的“形状的主要模式”的通用性很高,可用于其他种类和形状的零件。也就是说,即便生产线发生大规模的变更,AI也能灵活应对。通过运用AI,包含验证程序在内的修改时间,从以往的7天缩减到了8个小时。肥冢哲男说:“晚上学习AI后,次日清晨就能制定出新的计划。”今后,富士通计划将AI灵活应用于机器人操作程序等领域。
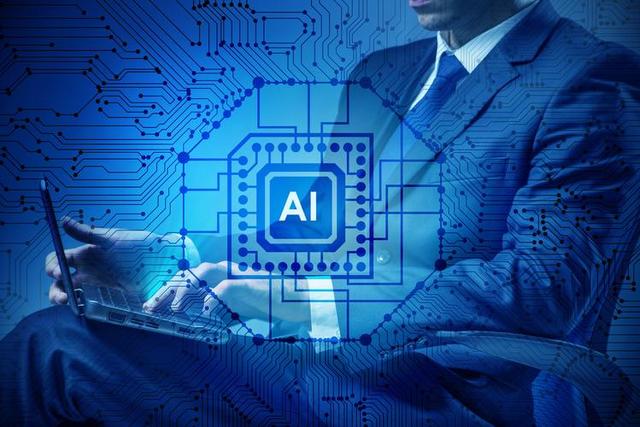
瑞萨电子:让AI像熟练技工一样判断优劣
瑞萨电子主要致力于在工厂中应用AI。目前,瑞萨电子正在研发用于FA机器的、组合半导体和AI的解决方案。试验及应用场所,位于其生产子公司瑞萨半导体制造公司的那珂工厂(以下简称“瑞萨那珂工厂”)。
成为FA设备的头脑原本,瑞萨电子的解决方案依据的是“边缘计算”这一概念。总的来说,边缘计算,是指在网络末端(边缘)设置的服务器上,分散处理以大数据分析为代表的大规模计算。一般的大数据分析,会将网络末端收集到的数据集中到云服务器中,进行集中处理。但是,生产现场对实时性的需求很高,将所有数据收集到云服务器中,或基于分析结果从云服务器中控制末端是不现实的。必须使可编程逻辑控制器(PLC)、I/O单元等末端的FA设备(边缘装置)具有高度的数据处理功能,从而对大数据进行分散性的处理。于是,为塑造边缘设备的“头脑”,瑞萨电子导入了AI。瑞萨电子拥有统一处理CPU、实时操作系统OS和产业用以太网通信功能的LSI技术——“R-IN引擎”。
瑞萨电子针对“RIN引擎”开发出了新的AI模块,使产业用LSI适用“R-IN引擎”,并能进行高度的数据处理。其目的,是将这种产业用LSI普及到多个边缘设备中。“R-IN引擎”对以往在软件中实现的实时操作系统OS及产业用以太网通信功能进行了硬件化,从而提高了CPU的数据处理性能。由此产生的余力,被转移到了AI模块的资源库,确保了高实时性和高数据处理能力。在Al模块的开发中,瑞萨电子与CompassIntelligence公司(总部位于东京)展开了合作。在瑞萨那珂工厂,AI被用于判断半导体生产流程的好坏。具体来说,就是测量等离子蚀刻工序中的等离子发光强度(电压),分析绘制在时间轴上的波形,以确定加工质量的好坏。等离子体的发光强度与晶片的加工量密切相关,因此可以从其波形推测出加工质量。
比较实际测量值(输入波形)与学习后的AI得出的预测值(再生波形),对两者之间的差的累积值(错误波形)进行阈值管理。想让AI判断优劣,必须先输入大量的良品和不良品数据。AI将基于该数据,学习良品模式。向完成学业的AI输入实际测量的数据时,AI会基于实际输入值和良品模式,模仿该波形输出另一波形。如果是良品,那么输入波形与再生波形基本一致。如果是不良品,则会产生偏差。AI通过对两者之间的差的累积值进行阈值管理,判定优劣。
担负繁杂工作以上案例,还充分利用了CPU处理性能高的“R-IN引擎”的特点。在一般的FA设备中,对等离子体的发光强度进行取样是以1秒为单位的。而采用“RIN引擎”的FA设备可进行50毫秒(1毫秒=0.001秒)的采样,大大提高了判定结果的精度。这样的精度,不仅可以用于判定产品优劣,还可以用于预先维护生产设备等方面。瑞萨半导体制造执行董事井上修一说:“我现在觉得,繁杂的业务已经可以交给AI去处理了。”
评论排行