自动化在化工领域的应用
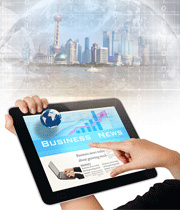
你知道一个化工工艺流程安全运行需要多少装置?需要多少设备吗?你知道一个化工工艺流程是怎样安全运行起来的吗?我们一起了解一下具体情况吧。
一起了解一下石油化工工艺流程中的一个"简单"装置
自动化技术是城市轨道交通领域中最重要的技术之一,对城市轨道交通建设起着至关重要的作用。像嵌入式系统、SCADA、PLC、现场总线、变频器、传感器、人机界面、工控机等自动化产品都被广泛应用到轨道交通建设中去,在车辆管理、安全监控、电力检测以及保障轨道交通正常运行等方面发挥着不可小觑的作用。比如红绿灯就是通过可编程控制器控制的。
以下图为炼油厂燃料油系统

接下来我们一起看一下炼油厂燃料油系统中的加氢裂化装置。
我们先对加氢裂化装置进行一下简单介绍。加氢裂化是重质油轻质化的一种工艺方法。以减压馏分油为原料,与氢气混合在温度400℃左右,压力约17MPa和催化剂作用下进行裂化反应,生产出干气、液化石油气、轻石脑油、重石脑油、航空煤油、轻柴油等产品。
加氢裂化、加氢精制装置示意图

在这个简单装置中,用到了各种换热器、冷却器、省能器、再沸器、冷凝器、洗涤塔、浓缩塔……大约100个设备。
以上仅仅是炼油厂燃料油系统中的加氢裂化装置中的一些设备。可想而知,整个石油化工工艺流程需要多少设备呢?除此之外,还要将这些设备连在一起,进行检测、观察、分析……才能保证整个燃料油系统的安全运行。想象一下,如果人为的去做这些事情,会是什么样的情景呢?这需要多少人力物力呢?但是有了自动化,一切都变得方便多了。
自动化在化工生产中的发展
20世纪40年代以前,化工生产已采用了自动化装置,但是没有系统的理论指导。40年代中期经典控制理论开始应用于化工生产。50年代开始实现过程控制,用电动和气动式模拟调节器实现单参数定值调节。60年代出现了以组合仪表进行集中检测和控制的系统,并开始利用计算机对整个系统或装置进行集中综合自动控制。70年代产生了信息集中化、控制分散化的集中分散型计算机多级控制系统,采用了定值控制、前馈控制、多变量控制、自适应控制和最优控制等方法,并利用微型计算机进行企业管理,包括控制、信号报警、生产调度、安全管理等方面。
自动化在化工仪表中的作用
自动化控制在化工仪表起到了什么作用呢?其主要采用先进的微电脑芯片及技术,减小了仪表的体积,并提高了仪表的可靠性及抗干扰性能。实现真正的以逸待劳以及待人的目的。主要作用体现在以下几个方面:
(一)仪表有了可编程功能
计算机的软件进入仪表,可以代替大量的硬件逻辑电路,这叫硬件软化。特别是在控制电路中应用一些接口芯片的位控特性进行一个复杂功能的控制,其软件编程很简单(即可以用存储控制程序代替以往的顺序控制) 。而如果带之以硬件,就需要一大套控制和定时电路。所以软件移植入仪器仪表可以大大简化硬件的结构,代替常规的逻辑电路。
(二)仪表有了记忆功能
以往的仪表采用组合逻辑电路和时序电路,只能在某一时刻记忆一些简单状态,当下一状态到来时,前一状态的信息就消失了。但微机引入仪表后,由于它的随机存储器可以记忆前一状态信息,只要通电,就可以一直保存记忆,并且可以同时记忆许多状态信息,然后进行重现或处理。
(三)仪表有了计算功能
由于自动化化仪表内含微型计算机,因此可以进行许多复杂的计算,并且具有很高的精度。在自动化仪表中可经常进行诸如乘除一个常数、确定极大和极小值、被测量的给定极限检测等多方面的运算和比较。
(四)仪表有了数据处理的功能
在测量中常常会遇到线性化处理、自检自校、测量值与工程值的转换以及抗干扰问题。由于有了微处理器和软件,这些都可以很方便的用软件来处理,一方面大大减轻了硬件的负担,又增了丰富的处理功能。自动化仪表也完全可以进行检索、优化等工作。
自动化在化工工艺流程中的作用
自动检测与控制——化工生产过程经常要在高温、高压下进行,某些物料易燃、易爆,具有毒性和腐蚀性,同时反应的机理和过程十分复杂,因而对自动化控制生产过程的要求特别迫切。为了实现过程自动化,首先应对生产过程中的主要工艺参数如温度、压力、流量、液位、成分等进行自动检测,获得准确可靠的数据。检测是通过各种敏感器件来完成的。有些参数测量还需要靠微型计算机辅助,如饱和蒸汽流量测量中的湿度和压力的自动补偿。有时还用模型化的方法来进行特殊变量的测量和用状态观测的方法来进行某些变量的预估。一些高温、高粘度、大流量和低温的自动测量技术已取得较大的进展;利用参数辨识和相关技术的间接测量方法也在石油、化工的特种参数测量中开始应用。
测量所得的数据是对生产过程进行自动监视和控制的基础。例如,控制系统的调节作用就是根据所得到的数据进行比较、运算,然后发出指令操纵调节阀而实现的。化工生产过程自动控制包括单参数的控制和整个装置或系统的集中综合控制。化工自动化控制的特点在于动态和反馈。系统工作总是在稳态附近变化,波动是由于干扰引起的,控制的目的是使系统在预计的最大偏离的条件下恢复到稳态。在闭环控制系统中还将控制效果的信息反馈到控制器去进行比较,以改善控制的效果。一般改变反馈的大小、形式或方式,往往就可以改变控制的结果。在现代化工生产过程的自动控制中所采用的控制方式有:前馈控制、反馈控制、多变量解耦控制、状态反馈控制、克服大滞后的预估补偿控制、采样控制、最短时间控制和线性最优控制等。针对石油、化工过程的时变、随机和状态难于直接测量等特点,还采用随机最优控制、自校正控制、自适应控制、状态观测和卡尔曼滤波技术等。电子计算机在自动控制中主要完成信息的存储、处理、逻辑判断、动态过程分析、决策、控制和事故诊断的功能。例如,在自动信号联锁保护系统中,应用信号联锁和计算机的上述功能对化工企业的安全生产实行声光信号指示、屏幕显示、事故操作指导和联锁切断保护等。
系统仿真——数字仿真技术在化工生产过程自动化中已广泛应用,例如用于分析研究系统的动态和静态行为,寻求最优控制方案、优化操作条件,为设计新控制系统提供依据以及培训操作人员。仿真的质量取决于所建立的数学模型的准确性。但由于石油、化工过程的复杂性,仿真技术的应用受到了一定限制。但是随着社会技术的进步,在不久的将来这些困难会克服的。
ESD系统在化工领域的应用
对于石油和化工生产装置来说,设置独立于控制系统的安全联锁是十分有必要的。而ESD系统就是独立于主控制系统的,其安全级别高于主控制系统。在正常情况下,ESD系统处于静态,不需要人为干预。它作为安全保护系统,凌驾于生产过程控制之上,适时在线监测装置的安全性。当生产装置出现紧急情况时,不需要经过主控制系统,而直接由ESD发出保护联锁信号,对现场设备进行安全保护,避免危险扩散造成巨大损失。该动则动,不该动则不动,这是ESD系统的一个显著特点。
高可靠性的ESD系统不仅能保证设备安全无干扰地运行,还能为装置提供一体化的解决方案。同时这个系统还兼具准确的记录功能,内部的事件报警器可以清楚地记录下紧急停车过程中每一个操作步骤和报警事件,为专业人员查找事故原因和事故部位提供了第一手材料。
目前,国内很多大型乙二醇、环氧乙烷等危险等级高的装置都采用了ESD紧急停车系统,实现了紧急状况下阀门自动开、关,使系统退守到相对安全的状态。这可以在很大程度上避免操作人员由于紧张慌乱、判断不准确等原因引起的误操作,使紧急停车过程变得安全、准确、简单,降低了事故发生率和危害程度。
通过以上内容,你了解化工工艺之所以安全运行的原因了吗?
化工生产处理的物质往往具有易燃、易爆、腐蚀性强和有毒害物质多等特点,且生产装置趋向大型化,一旦发生事故,波及面很大,对国民经济及所在地区的人民安全,带来难以估计的损失和灾害。由于自动化在化工工艺的应用,减少了化工工艺事故的发生。近几年,虽然化工事故没有完全避免,但是小甄相信,随着科技的不断进步,自动化会更广泛的应用于化工工艺,使化工工艺流程更加智能化,化工工艺流程更加安全,化工事故会避免的。
对此如果您有什么独到见解,欢迎加入自动化企业QQ: 4006876636 品牌观察讨论组。
>> 活动介绍 | |||
---|---|---|---|
1. 2012年度自动化行业最具影响力品牌评选介绍
2. 2012年度自动化行业最具影响力品牌评选规则 3. 2012年度自动化行业最具影响力品牌评选 |
----- 自动化网 自动化行业品牌研究室
评论排行