【山东新智造】国家级智能制造试点示范项目巡礼第四期:钢铁冶金行业优秀案例
【ZiDongHua 之方案应用场收录关键词:智能制造 高质量发展 数字孪生 工业互联网 】
【山东新智造】国家级智能制造试点示范项目巡礼第四期:钢铁冶金行业优秀案例
山东新智造
根据国家《“十四五”智能制造发展规划》要求,工业和信息化部已连续3年开展智能制造试点示范行动,遴选一批智能制造示范工厂和优秀场景,在各行业、各领域选树一批排头兵企业,推进智能制造高质量发展。近年来,我省积极推进企业开展“智改数转”,不断完善“市级-省级-国家级”智能制造示范项目梯次培育体系,取得了良好成效。目前,省级智能工厂(数字化车间、优秀场景)977个,累计培育国家级示范工厂35个、优秀场景108个,数量位居全国前列。
为进一步宣传智能制造典型企业和优秀案例,推广先进经验,现开展国家级智能制造试点示范项目巡礼宣传活动,展示优秀企业智能制造转型发展经验,共同学习提高,打造山东“智造”升级版。本期选择钢铁冶金行业优秀案例,让我们走进石横特钢集团有限公司、山东钢铁集团永锋临港有限公司两家企业,感受山东“智造”魅力。
一、石横特钢集团有限公司
(一)企业基本情况
石横特钢集团有限公司地处山东省肥城市境内,是一个集炼铁、炼钢、轧钢、焦化、化工、物流、机械制造、科研、资本运作为一体的大型钢铁联合企业,占地5500亩,现有职工7000多名,综合经济实力连续多年跨入中国企业500强之列,被评为国家级智能制造示范工厂揭榜单位、国家级绿色工厂、高新技术企业、全国和谐劳动关系创建示范企业、国家企业技术中心。
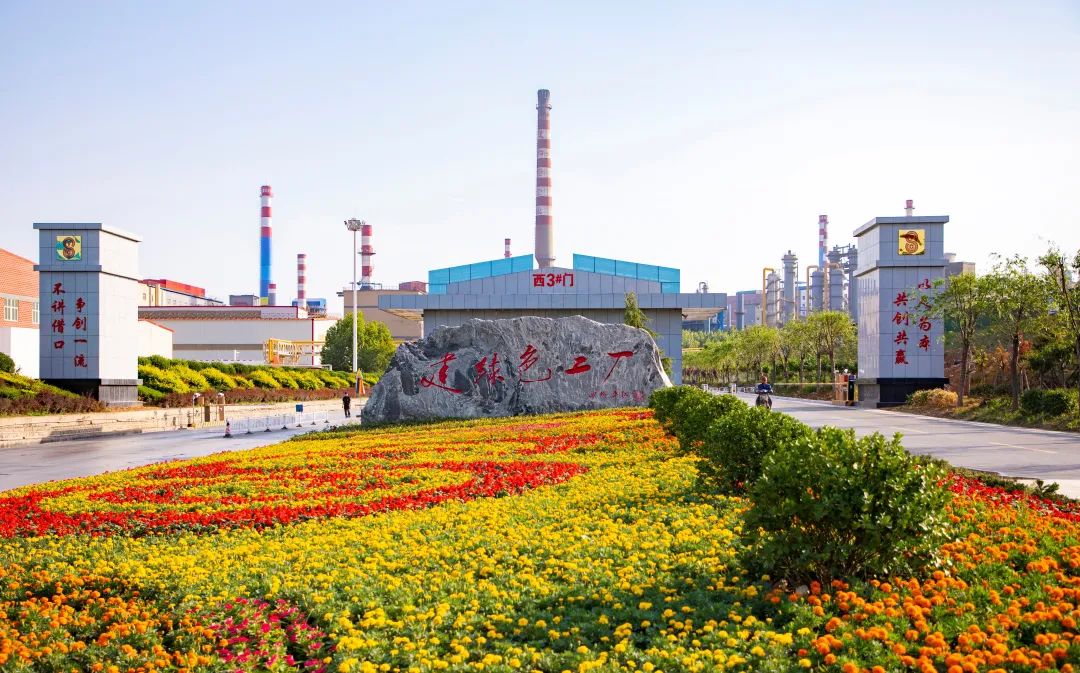
2016年斥资20亿元重组了肥城阿斯德化工,开启了钢铁、化工联合的新模式,实现了资源的综合利用“变废为宝”;2019年入股了泰安华鲁锻压机床,推动了跨行业,跨地区的高效组合,实现了产业链的上下游延伸,达到了1+1>3的战略效果。2020年,依照山东省“两基地四集群”钢铁规划,泰安特种建筑用钢产业集群一期工程顺利投产。截至目前,锚杆钢筋全国市场占有率超过60%,是全国最大的生产供应基地,电力角钢市场占有率第一位,在国内市场处于行业领先地位。
(二)智能工厂建设先进经验
精品特种钢全流程智能示范工厂是泰安特种用钢产能置换项目,由2座1460立方米高炉生产线、2座转炉及连铸生产线、2条烧结生产线、2条棒材生产线组成。利用“可视化”高炉系统、远程支撑系统、一体化炼铁管控平台等实现工艺流程、物质能源、设备信息精确控制。引进国际先进的循环流化床半干法脱硫、高效SCR脱硝、微克级布袋除尘等技术,配套煤气、蒸汽、炉渣、铁碳元素和工业用水五大循环回收利用工程,以此来打造“绿色钢城”。
1.数字孪生工厂
石横特钢精品特种钢全流程智能示范工厂在建设过程中,在热连轧过程、智能料场、转炉炼钢、方坯连铸、棒材加热、棒材轧制等多个环节应用建模仿真、多模型融合等技术,对实体系统和设备进行了量化表达,构建了装备、产线、车间、工厂等不同层级的数字孪生系统,通过物理世界和虚拟空间的实时映射,将工艺与量化的物理实体模型结合起来,形成对最终产品质量的数字化表达,提高模型预测与设定精度,并能够基于模型进行数字化运行和维护。
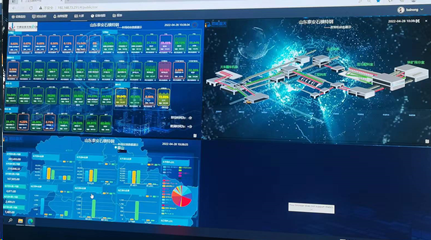
智能料场自动化数字孪生工厂
2.生产计划优化
在生产计划优化环节,构建完善公司级ERP企业资源管理系统,并与生产管理系统、物流系统、质检系统及各车间L2平台系统进行了集成。建立统一的数据收集交换平台,实现ERP与MES、远程智能计量等不同系统间数据一贯制管理;建设资源计划平衡平台,实现资源在产线间成本最优、产能相对平衡的精益化生产;建设物料结算平台,实现采购、销售的统一结算管理。应用了订单管理、生产计划/排程、生产跟踪、调度与实绩管理、半成品/成品库存管理、厂内物流计划与调度管理等功能,实现基于采购提前期、安全库存和市场需求的生产计划优化。
3.先进过程控制
在工厂的各个环节部署了智能制造装备,建设了全国首套连铸坯智能定重定尺系统,实现对炼钢厂特定铸机进行定制性开发,通过精准、智能、闭环的在线定重系统解决钢坯重量波动,使定重精度±6kg达到85%,±10kg达到90%以上,铸坯定重效果良好,定重合格率提升10%以上。
建设了国内最先进的轧钢加热炉智能燃烧系统。该系统针对蓄热式加热炉燃烧特点,结合加热炉燃烧烟气残氧及CO检测仪表、钢坯温度检测仪表以及先进的加热炉二级系统、燃烧数学模型、燃烧优化系统组建成加热炉智能控制系统平台。
手机端监控加热炉生产及设备情况
4.质量精准追溯
建设了质量管理系统,通过生产仿真、质量设计与实时分析、订单跟踪等,采集产品原料、设计、生产、使用等质量信息,实现产品质量全生命周期控制,确保对市场做出快速响应,处理质量异议时间能够控制在一周内。
计量管理系统
5.设备在线监测
集成了智能传感、机器视觉、故障检测等技术,构建了统一的设备管理与维检系统,通过专业化设备管理及维检、智能电网管控等方式,利用电网潮流控制技术、变电站监控技术、电网管控技术,实时监测设备状态,判定设备运行情况,开展性能分析和异常报警,提高了控制效率,避免非计划停机,为“设备零故障管理”提供有力保障。
智能电网管控系统主画面
变电站监控系统界面
6.能效平衡与优化
建设了能源管控中心,基于综合能源管理系统,实现从能源数据采集-过程监控-能源介质消耗分析-能耗管理等全流程的信息化管理,实现企业优化能源介质平衡,提高能源介质的回收和梯级利用水平,保障多能源介质的协同平衡。
手机APP实时数据检测
7.安全风险实时监测与应急处置
依托感知装置、安全生产管理系统、安全生产全要素管理系统、特殊作业全过程系统和人员自动定位系统,建设了双重预防机制平台,基于智能传感、机器视觉、特征分析、专家系统等技术,动态感知、精准识别危化品、危险环节等各类风险,实现了安全事件的快速响应和智能处置。
安全管控中心
安全管控平台人员自动定位系统
8.污染监测与管控
结合污染源清单等先进技术,建立全厂全面的排放源清单管理、污染监控、污染监测、治理设备监控、生产状态监控的全过程一体化管控平台,将无组织排放“有组织化”管理,实现无组织排放全过程管控,常态化管控,治理过程可追溯可核查。本平台对全厂无组织排放源清单中所有监测、治理设备进行集中管控,并记录各无组织排放源点相关生产设施运行状况、收尘、抑尘、清洗等治理设施运行数据、颗粒物监测数据和视频监控历史数据。
超低排放管控平台视频墙
地图系统
(三)智能工厂建设成效
1.工厂建设完成后,吨钢级的产量已达到每小时300吨,产量国际领先,综合生产效率提升68%,设备综合利用率提升31%,运营成本下降47%,研发周期缩短53%,产品不良率下降77%,资源综合利用率提升31%,销售增长35%,各项经济技术指标已达到国际一流水平。
2.工厂全部投产后,钢产能达到465万吨,产能、产值、利润翻番,库存周转率提升71%,订单准时交付率提升11%,其研发的产品也将于近期形成批量生产,石横特钢也将因此成为国内最具竞争力的特种建筑用钢产业基地,年新增主营业务收入200亿元、利税30亿元。
3.工厂通过自动巡检、在线运行监测等方式,实现实时监测设备状态,判定设备运行情况,开展性能分析和异常报警,先进过程控制利用率达92%,设备综合利用率提升19%,经济效益显著。
4.整个工厂生产单位产品综合能耗降低12%,单位产品二氧化碳排放量降低8%,同时带动了其他场景的智能化建设,经济效益明显。
二、山东钢铁集团永锋临港有限公司
(一)企业基本情况
山东钢铁集团永锋临港有限公司位于山东省临沂市临港经济开发区精品钢园区,成立于2019年4月9日。项目总投资约350亿元,主要包括规划年产1000万吨精品钢和配套400万吨焦化及精细化工项目,总占地7000亩左右。分两期建设,一期项目已于2021年7月份投产。一期项目总占地面积约为4655亩,建设总投资136.6亿元,2021年7月份投产,具备年产270万吨精品长材的能力。主要综合配套设施有1台500平方米烧结机、2座1350立方米高炉、2座120吨转炉等。当前正在积极推进二期项目建设,实现精品长材及精品板材生产全覆盖。产品定位中高端,有优质碳素结构钢、低碳钢、低合金高强度结构钢等。在产业链延伸方面,通过配套先进的表面处理工艺,95%以上的产品可以进行深加工,实现由钢铁产品向钢铁制品转型。
公司2022年被国家生态环境部评为A级绩效企业,成功入选山东省工业旅游示范基地。2022年12月30日《世界金属导报》将永锋临港公司打造的全球首个统一平台全流程数字钢厂纳入“2022年世界钢铁工业十大技术要闻”之中。2023年1月通过国家工信部等四部门联合公告,评为“国家级全流程智能制造示范工厂揭榜单位”。在此基础上,公司积极打造以智慧建筑、智能制造、智慧物流及智慧服务为产业主题的智能制造产业园,打造全球绿色低碳高质量发展的样板。
(二)智能工厂建设先进经验
1.建设永锋临港智控中心
通过自动化网络技术把以往分散在现场的10大工序和四大调度全部集中在一起,实现了5公里以外的远程操控,同时通过“生产、物流、能源、设备、安防”五调合一,实现了跨工序、跨区域、远距离、大规模集控、无边界协同交融和大数据决策的生产一体化智能管控,形成公司临港基地统一的生产操作中心、调度中心、应急指挥中心。
永锋临港智控中心
2.打造全球首个统一平台全流程数字钢厂
基于统一工业互联网平台,横向贯通各生产工序和管理部门,纵向打通从现场PLC到集团ERP系统的数据链路,开发了12个大智能应用,2010个功能模块,为钢铁生产从原料进厂、库存、加工到成品出厂每个生产环节提供了全面数字化支撑。借助工业互联网平台赋能生产经营,实现了数字化透明生产,各工序之间、部门之间实现无边界协同,创造了巨大的经济效益。
全流程工业互联网平台架构
3.完善IT基础设施
建设覆盖全厂的网络架构,围绕工业互联网平台,建设了遍布全厂的37个机房和网络,连接现场3万多个设备,采集28万点数据。
完备的数据网络系统
4.打造生产管控系统
为应对复杂多变的市场形势,公司秉持“低库存、快周转”方针,通过智能配料、智能排程等智能化应用,结合原料和钢材两头市场变化,采用遗传算法进行大数据寻优,计算出最佳的生产配料、计划排程,实现生产和市场的联动,实现低库存快周转,实现极致成本、极致效益,进一步增强持续盈利能力和企业核心竞争力。
全厂生产管控总览图
按“应采尽采”原则,大量采集生产经营相关数据,通过数据分析,服务生产经营。每日产生15亿条生产过程数据记录(截图显示2022年5千亿条,目前已远超万亿条)。
数据资产总览图
5.关键设备状态监测预警
应用智能设备对全公司关键设备进行状态监测预警,及时发现和消除设备的早期隐患。通过备件编码统一,实现集团多基地备件共享,降低备件库存资金。
全厂设备管控界面
6.环保在线监控
临港一期项目累计环保投入23亿元,借助环保智能应用,将全公司200多个环保在线测点集中监控,采用源头控制及末端治理等技术,按照内控标准进行预警管理,减少污染物排放,目前颗粒物控制在3毫克/立方米、二氧化硫控制在2毫克/立方米、氮氧化物控制在20毫克/立方米左右,达到超超低排放水平,已通过国家生态环境部A级绩效企业评定。
全厂环保管控界面
7.建设智能料场
采用数字化、无人化技术,实现智能化物料运输流程控制和堆取料机、刮板机等大型设备复杂作业的无人化,精简操作岗位。堆取料规整,减少抛洒,提高料场空间利用率,减少设备无效动作时间,降低电耗。
智能料场界面
8.铁区智能应用系统
把铁前四大系统的生产数据关联起来,结合冶金机理、大数据算法开发了混匀-烧结-球团-高炉一体化配矿及带成分入炉等跨工序数学模型,基于工序智能应用构建数据分析体系、合规管控体系及安全运行体系,促进了铁区生产从分散管控向以高炉为核心的铁区一体化智能管控的转变,实现绿色化、低耗化、稳定化、高效化的铁前生产。
铁区一体化智能管控界面
通过RFID技术,动态跟踪铁水运输过程,实现自动计量,同时分析作业瓶颈,优化铁水调度,提高铁水罐周转率(目前单日可达6.25次),减少铁水钢水温降。
工艺铁路管控界面
搭建智能炼钢系统,围绕效率、成本、质量,从时间、温度、成分、重量四个维度对炼钢进行智能管控,其中的生产节奏管控将转炉-精炼-连铸15个操作步骤数字化,量化到秒,实现生产节奏的跟踪、预测、分析,及时预警支撑调度,分秒必争,发现瓶颈环节,持续改善,最后分析给出每一个作业环节的时效优化建议。
智能炼钢系统界面
打造智慧转炉系统,利用工艺模型、智能化、自动化技术,降低渣料、合金消耗,提高终点一次命中率。开发了铸坯跟踪、仿真剔坯模型,实现钢坯的直轧和热送。基于铸坯的按支跟踪,实现定尺切割优化,提升定尺率,每年降低钢坯消耗。
智慧转炉系统界面
打造轧钢智能仓储系统,行业内首次采用图像识别技术,实现棒材在装卸过程中的扫码识别,在不影响生产节奏的前提下,解决棒材产线和仓储环节无断点跟踪的行业难题,减少出入库人工扫码工作量,实现了轧钢棒材仓储的数字化,实现棒材从成品下线到装车发运的智能调度。
智能仓储系统
(三)智能工厂建设成效
1.通过精益运营和智能制造,大大提高了劳动生产效率,一期项目投产后,人均产钢1700吨/年,二期项目投产后人均产钢超过2000吨/年,处于行业领先水平。炼铁高炉利用系数4.15,铁水消耗最低704㎏/t。转炉班冶炼炉数19炉、连铸拉速4.6m/min,各项经济技术指标达到全国领先水平。
2.通过生产管控系统,每年可降低成本5600万元。设备智能应用系统上线后,故障时间月度平均下降为118.8min、维修费用月度平均41.34元/吨钢,每年可降低备件库存资金2000万元。
3.智能料场系统上线后,精简操作岗位50个,提高料场空间利用率20%;3D自动扫描提高盘库效率90%;减少设备无效动作时间,每年降低电耗240万元。
4.铁区智能应用系统上线后,高炉日平均产量提高300吨,高炉燃料成本降低12.8元/吨。通过铁钢界面管控系统,提高铁水罐周转率单日可达6.25次,减少铁水钢水温降9.91℃,由此全年可降成本3500万元。
5.通过钢轧界面开发了铸坯跟踪、仿真剔坯模型,实现钢坯的直轧和热送,每年可降低煤气消耗450万元。通过轧钢智能应用系统,基于铸坯的按支跟踪,可提升定尺率0.15%,每年降低钢坯消耗300万元。通过轧钢智能仓储系统,可减少90%以上的出入库人工扫码工作量。
来源:装备产业处
我要收藏
个赞
评论排行