“关灯工厂”热火朝天 疫情倒逼企业自动化改造提速
近日,位于重庆两江新区的长安福特三工厂内,一辆刚刚组装完成的长安福特锐际从组装线缓缓驶出,成为两江新区推进有序复工复产以来首辆下线的整车。在恢复生产的长安汽车渝北工厂,生产车间里只有零星几名工人戴着口罩在操作、巡检,“主力军”是流水线上700多台工业机器人。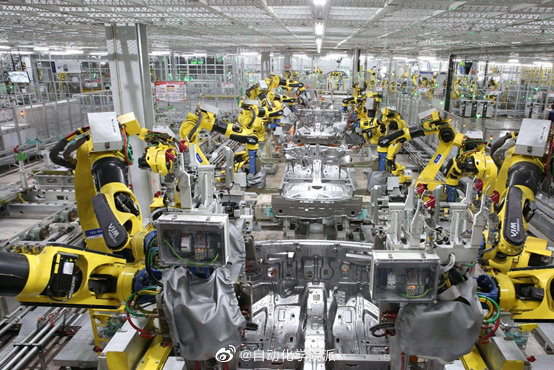
两年多来,智能化改造在重庆传统及新兴企业蔚然成风,智能制造及工业互联网带来的生产线人数减少、自动化生产、网络协同和产出效率高等特点,一批“关灯工厂”应运而生,在当前企业复工复产中正显现优势。
“关灯工厂”又可称为无人工厂,由于无需人工操作或仅需要极少的人,就可以在关灯的情况下实现正常运转而在近日备受关注。
从已复工的企业中,中企君发现:率先恢复正常运转的企业,不少都具有技术先进、自动化程度高的特点,比如“不停产”的宝钢股份上海宝山基地,即便是在春节期间也没停过工。
“不碰面生产”的黑科技
中国宝武钢铁集团有限公司是中国最大、最现代化的钢铁联合企业,总部位于上海和武汉,而宝山钢铁股份有限公司,也就是宝钢股份,正是他旗下的子公司。
今年1月,宝钢股份的上海宝山基地工厂首次入选世界经济论坛发布的全球“灯塔工厂”名单。面对疫情,这个新上榜的“灯塔工厂”有什么优秀的表现呢?
据行业人士透露,该工厂实现了覆盖全厂的智能制造,不仅提升生产效率,更在特殊时期,实现了疫情防控和稳产、高产的有效平衡。
春节假期以来,上海宝山基地的这个工厂没停过工。在厂区里,这些为数不多的工人依然戴着口罩坚守一线。而为他们带来保障的,除了口罩和各种防疫措施,还有遍布各道工序的机器人和自动化智能装备。
这个“灯塔工厂”的智慧制造都有何体现?比如冷轧车间,智能化改造前,冷轧生产线上工人众多:进料关口要站两名工人,负责把控钢卷质量;锌锅旁站两名工人,负责随时捞渣;成品出口站一名工人,检查成品质量;仓库里站两名工人,负责打捆贴标;此外,还需要至少一名的流动工人,随时应付突发情况。
据知情人士透露,以前产线上工人多,相互之间需要密切配合和互帮互助,但是若是遇到如今这样的疫情,就不太适合开工了。但是通过改造,冷轧车间内以前需要工人们去完成的那些最危险、最脏、最难的工作,比如进料、捞渣、出料、打包等,现如今都可以交给机器人们去完成。
目前,该基地有这样两条200米长的生产线,每条只需2、3名工人流动照看,基本可以实现不碰面生产。在生产线的一侧,有一个100多平方米的“六合一”操作室,分散坐着几名工人,他们通过电子幕墙,观察着生产线上的一切,而整个车间还不到十人。
如果生产线上真要遇到什么技术问题,工程师坐在家里就能解决。工作人员表示,手机中安装了智能远程操控软件后,通过手机操作,工程师不光能看到上海基地,就连远在三千公里外的宝钢湛江基地的情况也能清晰看到。
另外,宝钢股份的冷轧厂C008热镀锌智能车间,有一个业内早有耳闻的别称——黑灯工厂。
之所以得此名字,是因为原来的冷轧车间都是灯火通明的,经过2016年的改造后,原来由人工开的行车变成无人驾驶行车,也就不再需要行车工人现场驾驶,从而具备了24小时黑灯操作的条件。
据介绍,冷轧厂C008热镀锌智能车间实施各环节无人化运作后,吨钢能耗下降了15%,综合污染物吨钢下降30%、劳动效率提升30%,产能提升20%,加工成本下降10%。
除了“黑灯工厂”,在上海宝山的宝钢股份生产基地,还有六台无人驾驶框架车已参与到钢材转库、装船作业中,取代了原来的人工驾驶框架车,实现了“无人化”仓库与自动码头间的贯通。
“关灯工厂”的经济账
自2012年第一座关灯工厂在成都投入使用以来,富士康旗下的工业富联已经在深圳、成都、郑州、太原等地运行了6座关灯工厂,包括了精密机构件加工工厂、智能刀具加工工厂、精密组装、测试及包装工厂等。
“目前,六座关灯工厂已发展出设备监控维修预测、质量检测预判改进、能耗监控物流配置、产量优化智能调度、制程参数调整优化等多项基于工业现场的人工智能应用。”
到了2019年初,在瑞士日内瓦举办的达沃斯世界经济论坛上,富士康打造的深圳龙华“关灯工厂”入选世界“制造业灯塔工厂”,成为当时全球16家技术领先的制造业工厂之一。
据行业人士透露,他们位于深圳的这个“关灯工厂”已经基本做到熄灯状态下的无人自主作业,全部生产活动由电脑进行控制,生产第一线配有机器人而无需配备工人。另外,工业富联自主研发的雾小脑将海量设备连接至边缘计算及云端,应用到表面贴装、数控加工、机器人、组装测试、环境数据采集等场景,覆盖全行业数据采集。该“关灯工厂”最终使得生产效率提高30%,库存周期降低15%。
不开灯、更没有工人,那么该工厂的产线是如何工作的?
就拿数字化刀具切削生产线的来讲,其是在车间未开灯,仅有一排绿色的生产指示灯亮着的情况下就开始工作的。在机器确认了工作流程后,机器手将粗坯送入第一台机台,机台自动接收后关闭窗口,后由机台内的刀具进行切削。每个机台内部的上方悬着一个罗盘,标着数字1-20,每个数字下对应一把旋转刀具,而每一把刀承担一项任务。
工作人员透露,深圳的这个“关灯工厂”整个项目导入108台自动化设备,并已完成联网化。制程中SMT导入设备9台,节省人力50人,节省比例96%;ASSY导入设备21台,节省人力74人,节省比例79%;Test导入设备78台,节省人力156人,节省比例88%。
疫情倒逼中国制造再升级
不同于电力、煤炭、油气等基础能源行业的“保供”特性,汽车、电子、消费品等工业领域的延期复工,往往“牵一发而动全身”。以汽车行业为例,零配件供应商因疫情生产受限,半数国内车企未能在2月10日如期复工。
面对上述局面,不少企业积极推动智能化、自动化,替代人工劳动力。
长安汽车的智慧工厂正尝试解决这一难题。通过“机器人打主力”,工厂自动化率达90%以上,生产中的汽车经自动传送装置依次被运送到下一道工序,物流小车往返都实现自动运输,只有零星的工人佩戴口罩来回操作、巡检……智慧工厂比传统汽车制造工厂减少操作工人56%,生产效率提升20%,避免了工人扎堆。
而同时拥有两座灯塔工厂的海尔近日透露,除武汉3家工厂外,海尔智家其余工厂均已于2月10日复产复工。目前海尔冰冷产业线、洗涤产业线、空调产业线、热水器产业、厨电产业线等均预计将于2月底全部达产。
“作为以用户为中心的大规模定制模式的典范,通过部署可扩展的数字平台,实现企业与用户资源和供应商资源的端到端连接,生产效率提升了28%。”这是官方给予海尔沈阳冰箱互联工厂成功入选灯塔工厂的评价,而这句话的内容也正是其工业互联网能力的体现。
在江西,为缓解医疗物资短缺难题,诸多企业也在加大自动化设备的引进,扩大产能,聚焦医用口罩、消毒液、红外体温测量仪,着力解决医用物资短缺的困局。
在浙江嘉兴,福莱特集团玻璃生产车间内,流水线旁一台台机械臂完成了一块玻璃从生产到成品包装的流程,企业自动化程度达到了70%。
“疫情过后,更多的企业愿意去做自动化。不管是中小企业还是大客户都会更加意识道自动化、无人工厂的重要性。”机器人制造商埃斯顿一位管理层表示。
最新数据显示,工业机器人行业景气拐点将至。2019年12月,国内工业机器人产量20014台,同比增长15.3%,结束了连续13个月的增速下滑。加之从减速器订单等前置指标以及相关行业指标的佐证,工业机器人行业转暖信号已现。
值得一提的是,在半导体行业,工厂高度自动化特征尤为凸显,短期半导体行业受疫情影响有限。安信证券研报分析,此次疫情导致半导体产业链短期内生产面临承压,消费有所滞后,PCB厂商会受到或多或少的影响。但半导体行业生产自动化较高,企业多地布局,疫情对长期半导体行业发展规划和5G产业布局的影响有限。
可以预见,此次疫情也将大大缩短传统产业尤其是制造业数字化、智能化的过程。人工智能、大数据、云计算等将再次迎来爆发式增长,智能工厂、自动化工厂的普及加快,或将是“中国制造”的又一次重大变革。
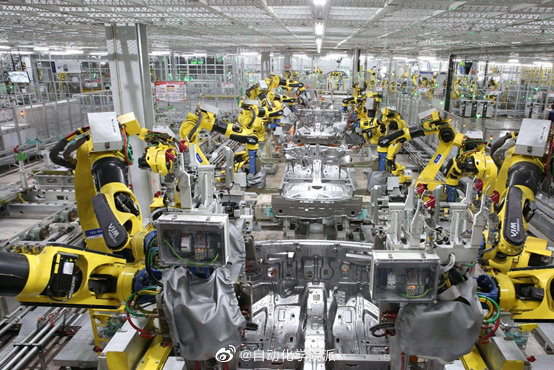
“关灯工厂”又可称为无人工厂,由于无需人工操作或仅需要极少的人,就可以在关灯的情况下实现正常运转而在近日备受关注。
从已复工的企业中,中企君发现:率先恢复正常运转的企业,不少都具有技术先进、自动化程度高的特点,比如“不停产”的宝钢股份上海宝山基地,即便是在春节期间也没停过工。
“不碰面生产”的黑科技
中国宝武钢铁集团有限公司是中国最大、最现代化的钢铁联合企业,总部位于上海和武汉,而宝山钢铁股份有限公司,也就是宝钢股份,正是他旗下的子公司。
今年1月,宝钢股份的上海宝山基地工厂首次入选世界经济论坛发布的全球“灯塔工厂”名单。面对疫情,这个新上榜的“灯塔工厂”有什么优秀的表现呢?
据行业人士透露,该工厂实现了覆盖全厂的智能制造,不仅提升生产效率,更在特殊时期,实现了疫情防控和稳产、高产的有效平衡。
春节假期以来,上海宝山基地的这个工厂没停过工。在厂区里,这些为数不多的工人依然戴着口罩坚守一线。而为他们带来保障的,除了口罩和各种防疫措施,还有遍布各道工序的机器人和自动化智能装备。
这个“灯塔工厂”的智慧制造都有何体现?比如冷轧车间,智能化改造前,冷轧生产线上工人众多:进料关口要站两名工人,负责把控钢卷质量;锌锅旁站两名工人,负责随时捞渣;成品出口站一名工人,检查成品质量;仓库里站两名工人,负责打捆贴标;此外,还需要至少一名的流动工人,随时应付突发情况。
据知情人士透露,以前产线上工人多,相互之间需要密切配合和互帮互助,但是若是遇到如今这样的疫情,就不太适合开工了。但是通过改造,冷轧车间内以前需要工人们去完成的那些最危险、最脏、最难的工作,比如进料、捞渣、出料、打包等,现如今都可以交给机器人们去完成。
目前,该基地有这样两条200米长的生产线,每条只需2、3名工人流动照看,基本可以实现不碰面生产。在生产线的一侧,有一个100多平方米的“六合一”操作室,分散坐着几名工人,他们通过电子幕墙,观察着生产线上的一切,而整个车间还不到十人。
如果生产线上真要遇到什么技术问题,工程师坐在家里就能解决。工作人员表示,手机中安装了智能远程操控软件后,通过手机操作,工程师不光能看到上海基地,就连远在三千公里外的宝钢湛江基地的情况也能清晰看到。
另外,宝钢股份的冷轧厂C008热镀锌智能车间,有一个业内早有耳闻的别称——黑灯工厂。
之所以得此名字,是因为原来的冷轧车间都是灯火通明的,经过2016年的改造后,原来由人工开的行车变成无人驾驶行车,也就不再需要行车工人现场驾驶,从而具备了24小时黑灯操作的条件。
据介绍,冷轧厂C008热镀锌智能车间实施各环节无人化运作后,吨钢能耗下降了15%,综合污染物吨钢下降30%、劳动效率提升30%,产能提升20%,加工成本下降10%。
除了“黑灯工厂”,在上海宝山的宝钢股份生产基地,还有六台无人驾驶框架车已参与到钢材转库、装船作业中,取代了原来的人工驾驶框架车,实现了“无人化”仓库与自动码头间的贯通。
“关灯工厂”的经济账
自2012年第一座关灯工厂在成都投入使用以来,富士康旗下的工业富联已经在深圳、成都、郑州、太原等地运行了6座关灯工厂,包括了精密机构件加工工厂、智能刀具加工工厂、精密组装、测试及包装工厂等。
“目前,六座关灯工厂已发展出设备监控维修预测、质量检测预判改进、能耗监控物流配置、产量优化智能调度、制程参数调整优化等多项基于工业现场的人工智能应用。”
到了2019年初,在瑞士日内瓦举办的达沃斯世界经济论坛上,富士康打造的深圳龙华“关灯工厂”入选世界“制造业灯塔工厂”,成为当时全球16家技术领先的制造业工厂之一。
据行业人士透露,他们位于深圳的这个“关灯工厂”已经基本做到熄灯状态下的无人自主作业,全部生产活动由电脑进行控制,生产第一线配有机器人而无需配备工人。另外,工业富联自主研发的雾小脑将海量设备连接至边缘计算及云端,应用到表面贴装、数控加工、机器人、组装测试、环境数据采集等场景,覆盖全行业数据采集。该“关灯工厂”最终使得生产效率提高30%,库存周期降低15%。
不开灯、更没有工人,那么该工厂的产线是如何工作的?
就拿数字化刀具切削生产线的来讲,其是在车间未开灯,仅有一排绿色的生产指示灯亮着的情况下就开始工作的。在机器确认了工作流程后,机器手将粗坯送入第一台机台,机台自动接收后关闭窗口,后由机台内的刀具进行切削。每个机台内部的上方悬着一个罗盘,标着数字1-20,每个数字下对应一把旋转刀具,而每一把刀承担一项任务。
工作人员透露,深圳的这个“关灯工厂”整个项目导入108台自动化设备,并已完成联网化。制程中SMT导入设备9台,节省人力50人,节省比例96%;ASSY导入设备21台,节省人力74人,节省比例79%;Test导入设备78台,节省人力156人,节省比例88%。
疫情倒逼中国制造再升级
不同于电力、煤炭、油气等基础能源行业的“保供”特性,汽车、电子、消费品等工业领域的延期复工,往往“牵一发而动全身”。以汽车行业为例,零配件供应商因疫情生产受限,半数国内车企未能在2月10日如期复工。
面对上述局面,不少企业积极推动智能化、自动化,替代人工劳动力。
长安汽车的智慧工厂正尝试解决这一难题。通过“机器人打主力”,工厂自动化率达90%以上,生产中的汽车经自动传送装置依次被运送到下一道工序,物流小车往返都实现自动运输,只有零星的工人佩戴口罩来回操作、巡检……智慧工厂比传统汽车制造工厂减少操作工人56%,生产效率提升20%,避免了工人扎堆。
而同时拥有两座灯塔工厂的海尔近日透露,除武汉3家工厂外,海尔智家其余工厂均已于2月10日复产复工。目前海尔冰冷产业线、洗涤产业线、空调产业线、热水器产业、厨电产业线等均预计将于2月底全部达产。
“作为以用户为中心的大规模定制模式的典范,通过部署可扩展的数字平台,实现企业与用户资源和供应商资源的端到端连接,生产效率提升了28%。”这是官方给予海尔沈阳冰箱互联工厂成功入选灯塔工厂的评价,而这句话的内容也正是其工业互联网能力的体现。
在江西,为缓解医疗物资短缺难题,诸多企业也在加大自动化设备的引进,扩大产能,聚焦医用口罩、消毒液、红外体温测量仪,着力解决医用物资短缺的困局。
在浙江嘉兴,福莱特集团玻璃生产车间内,流水线旁一台台机械臂完成了一块玻璃从生产到成品包装的流程,企业自动化程度达到了70%。
“疫情过后,更多的企业愿意去做自动化。不管是中小企业还是大客户都会更加意识道自动化、无人工厂的重要性。”机器人制造商埃斯顿一位管理层表示。
最新数据显示,工业机器人行业景气拐点将至。2019年12月,国内工业机器人产量20014台,同比增长15.3%,结束了连续13个月的增速下滑。加之从减速器订单等前置指标以及相关行业指标的佐证,工业机器人行业转暖信号已现。
值得一提的是,在半导体行业,工厂高度自动化特征尤为凸显,短期半导体行业受疫情影响有限。安信证券研报分析,此次疫情导致半导体产业链短期内生产面临承压,消费有所滞后,PCB厂商会受到或多或少的影响。但半导体行业生产自动化较高,企业多地布局,疫情对长期半导体行业发展规划和5G产业布局的影响有限。
可以预见,此次疫情也将大大缩短传统产业尤其是制造业数字化、智能化的过程。人工智能、大数据、云计算等将再次迎来爆发式增长,智能工厂、自动化工厂的普及加快,或将是“中国制造”的又一次重大变革。
我要收藏
个赞
评论排行