首钢冷轧:高端汽车板全业务精细协同管控智能工厂
首钢冷轧:高端汽车板全业务精细协同管控智能工厂
为贯彻落实国务院办公厅印发的《制造业数字化转型行动方案》,按照《“十四五”智能制造发展规划》任务部署,工业和信息化部等六部门联合开展2024年度智能工厂梯度培育行动,面向全国开展首批卓越级智能工厂评选工作,我市首钢冷轧、和利时、理想汽车等一批企业成功入选。为进一步宣传我市智能制造优秀成果,推动先进技术与成果经验推广,市经济和信息化局特设“北京智造巡礼——智能工厂篇”专栏,充分发挥卓越级智能工厂的示范引领作用,带动广大企业开展更高水平转型探索,系统深入推进智能制造。
当前,新一轮科技革命蓬勃发展,5G、人工智能等新技术加速融合,传统制造业亟需通过数字化推进智能生产、智慧运营、协同生态,不断提高生产制造效率和绿色环保水平。近年来,在国家部委和北京市大力支持和指导下,首钢集团着力夯实数字化转型基础,深化数智技术应用,强化人工智能驱动,加速产业转型升级,以数字化转型赋能企业高质量发展。
首钢股份冷轧公司(以下简称:首钢冷轧)以工业互联网建设为主线,积极开展智能制造探索和尝试,为数字化转型奠定了良好的管理及技术基础。首钢冷轧从业务、组织、技术三个方面开展智能化建设,应用5G、大数据、AI、机器视觉和机器人等先进技术,建立云、边、端技术架构和超融合算力平台,打造全生命周期的产销一体化管理体系,实现上下游互联互通。
首钢冷轧凭借智能制造先进技术的应用,以“高端汽车板全业务精细协同管控智能工厂”项目成功跻身国家首批“卓越级智能工厂”。这一重量级荣誉不仅是对首钢冷轧多年来在数字化转型领域不懈努力的肯定,更彰显了冷轧公司智能化转型升级的先进地位,为行业树立了标杆。
企业基本情况
首钢冷轧是首钢搬迁调整过程中匹配建设的国内知名高端汽车板生产基地。首钢冷轧积极争做国家智能制造排头兵,全力推动数实深度融合,探索新技术在传统钢铁行业场景下的大规模应用,创新数字化转型新模式,推动67个数字化应用场景部署落地,全面提升传统制造业数字化转型提效。
典型场景
场景1:知识图谱赋能,AI专家系统助力客户抱怨降低
板材冲压是汽车主机厂生产四大关键工序中的第一项,重要性不言而喻。冷轧公司汽车板用户共有超过1.7万种不同类型的零部件,冲压过程关联1500多个质量因素,以前出现缺陷后难以在短时间内找出根本原因,更无法提前预测。基于客户反馈、零部件信息、冲压工艺配方、汽车板生产流程参数和质量报告历史数据,并引入上千种质量相关因子,首钢冷轧开发了行业内首套汽车板材冲压知识图谱并部署AI专家系统。该系统既可以辅助快速分析和排除冲压故障缺陷,又能够为冷轧汽车板生产工艺优化迭代提供规范性建议,实现工艺风险早期预测。当前,在客户冲压零部件数量增加248%的情况下,排查冲压问题时间缩短83.3%,冲压质量相关投诉减少63.3%。
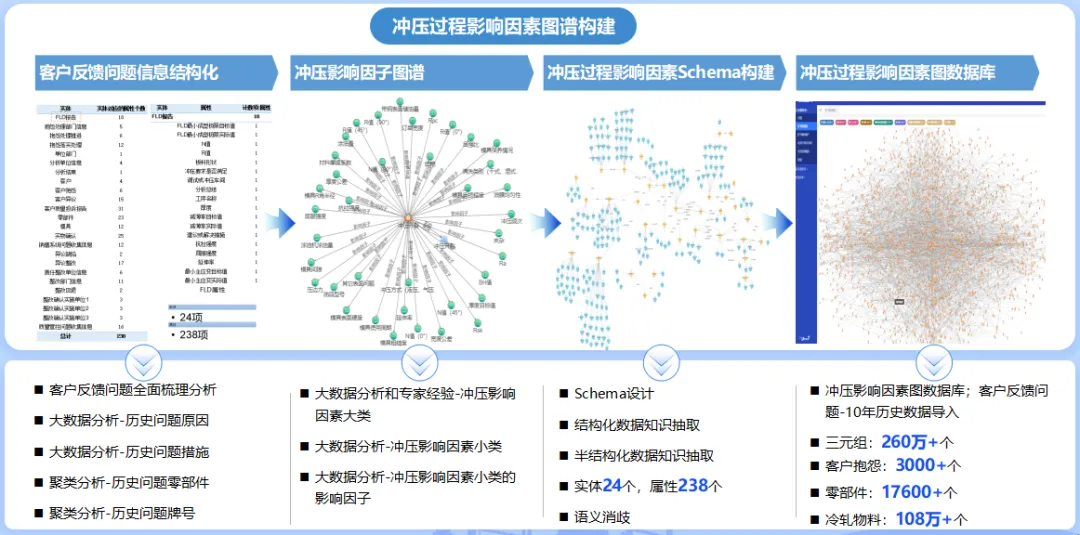
场景2:机器学习领航,工艺优化铸就品质提升
在冷轧公司70余家汽车主机厂用户中,个性化订单多达上千种,并且数量还在继续增加。以前接到新订单,产品工程师先凭经验进行“粗线条”工艺条件设计,产品上线测试生产时再手动反复调整参数寻找最优解,整个迭代环节平均时长约48小时,该过程产品缺陷率很高。
现在,基于7000万条生产大数据和先进的机器学习算法,首钢冷轧开发了一整套解决方案,包括80多个相关性模型,涵盖1200多条工艺参数、164种产品规格、26项产品特性和17类典型缺陷。新订单测试生产时模型可自动高效调整150多个工艺参数直至达到最优,全过程优化时间缩短97.9%,新产品缺陷率降低35.1%。

场景3:AI神经网络加持,镀锌工艺实现精准闭环
镀锌汽车板横截面类似“三明治”结构,上下表面为锌层,夹在中间的是钢板。锌层均匀性直接影响汽车厂用户使用效果,是镀锌汽车板关键质量指标。汽车板生产过程中,传统的人工锌层控制方法面临三大挑战:产线加减速时气刀参数调控滞后、前后两卷切换生产时锌层控制稳定性差、同一卷带钢锌层厚度横向不均匀。
结合神经网络深度学习技术,首钢冷轧开发部署了锌层厚度AI控制模型。模型根据订单需求、原料特性和产线实时工艺条件进行智能控制,当产线速度发生变化或者产品规格切换时,AI可在10毫秒内完成目标锌层厚度预测并动态调整最优参数,实现锌层厚度在带钢表面各方向上的高精度控制。最终产品锌层厚度偏差降低51.6%,缺陷减少46.4%,吨钢锌耗损失降低52.1%。

场景4:高阶分析驱动,生产线效率突破瓶颈
锌渣缺陷作为行业难题,严重制约镀锌汽车板生产线效能提升。带钢经过退火后高速进入锌锅完成表面“镀锌”过程,锌锅是产线的核心装备,内部承载着330吨高温熔融锌液,就像一个巨大的“黑箱子”。带钢中的铁(Fe)与锌液中的锌(Zn)和铝(Al)元素在一定条件下会形成固态金属化合物——“锌渣”。由于锌液始终处于湍流或涡流状态,会带着锌渣到处流动,当锌渣粘附在带钢表面时就会造成缺陷,导致产线降速或停机,依靠人工经验难于进行预测和控制。
首钢冷轧基于流体动力学和热力学特征建模,融合数字孪生和高阶分析技术,解析锌渣成因与带钢速度、锌锅流场和温度场等要素间关联条件;通过实时监测带钢速度、锌液温度等49组关键工艺和设备参数,开发出锌锅和炉鼻子智能控制模型。模型通过机器视觉检测带钢表面渣点数量和分布规律,实现与锌锅区域关键设备的闭环控制,抑制缺陷发生。产线OEE提高18.7%,汽车外板速度提升24.5%,缺陷识别时间缩短91.3%。
场景5:智能算法统筹,生产计划与排程精益升级
冷轧汽车板订单月均1230多种,超过14000个钢卷要在各条生产线上24小时连续运行,生产过程规格切换2000多次;同一产线前后相邻钢卷要满足50多项排程约束条件。以前,所有生产计划都依靠人工编排,效率低、准确性差,过程中要插入很多非订单过渡卷,导致有效产能损失和生产成本增加。
现在,一套包括41个多工序模型和24种先进算法的人工智能排程系统正式投入使用。系统支持6种生产场景调整和330条配置规则切换,可根据业务优先级进行智能决策,产品过渡损失降低32.5%,机组产能利用率提高24.4%,交货期缩短18%。
结语
首钢冷轧智能制造数字化转型,孵化出“标准统一、自主可控”的首钢工业互联网平台,支撑横向、纵向端到端业务需求,具备全业务场景的可扩展性。在今后工作中,首钢将积极贯彻落实国家及北京市关于发展新质生产力、推进数字化转型相关政策精神,积极推动技术创新,加快打造中国式现代化的首钢场景。
我要收藏
点个赞吧
平台转发数:1次
评论排行